Integrating 'green intelligence' into WHRPG
Published by Sol Klappholz,
Assistant Editor
World Cement,
WHRPG (Waste Heat Recovery Power Generation) technology refers to the technology that reutilises the wasted gas and heat exhausted from production through a WHR boiler during the production of cement, steel, coking, carbon, industrial silicon, etc. This process works by using the steam generated by the WHR boiler to propel a turbine and drive a generator.
The Chinese building materials industry has traditionally been energy intensive. As the third largest energy consumer after the metallurgy and chemical industries, it accounts for about 7% of the total national energy consumption, while the energy consumption of cement production has reached 75% of the energy consumption of the building materials industry. Under the increasingly strict national energy conservation and environmental protection policies, improving waste heat recovery and utilisation has become an important means of energy conservation and emissions reduction in the cement industry, among others. In today’s intelligent development of global industrial manufacturing, Sinoma-EC has always adhered to the concept of ‘making good use of resources to serve construction’, making ‘green’, ‘intelligent’ and ‘innovative’ the new labels of WHRPG technology.
Pioneering work in the field of WHR power generation
The 1980s was a period of rapid development of the high-energy-consuming industries represented by cement. The exhaust gas emissions of these industries simultaneously polluted the environment and wasted resources. In this situation, Sinoma-EC, which has cement waste heat power generation as its flagship business, came into being. Since undertaking the national 8th Five-Year scientific and technological research plan, Sinoma-EC has been committed to the research of waste heat power generation technology in cement plants. The waste heat power generation technology in cement production has also experienced a development process from high temperatures, with supplementary combustion to purely low temperatures. In recent years, with the introduction of concepts such as sustainable development, the circular economy, energy saving, emission reduction, and low-carbon economies, the market for waste heat recovery has continued to expand.
After more than 20 years of development and reform, Sinoma-EC has obtained a number of patents and proprietary technologies in the field of waste heat recovery. During this period, the company has successively undertaken the National Science and Technology Support Plan of both the 11th and 12th Five-Year Plans, the Tianjin Science and Technology Innovation Special Fund (Mayor’s Fund), and Tianjin ‘Killer’ products. These provincial and ministerial level science and technology projects have lead the company to develop advanced WHRPG technology. So far, Sinoma-EC has a state-recognised enterprise technology centre and a national engineering laboratory. It has also won second prize in the National Science and Technology Progress Award, whilst participating in the preparation of dozens of standards, holding qualifications in consulting, design, and general contracting. Sinoma-EC is an energy-saving service registered by the National Development and Reform Commission and the Ministry of Finance, as well as being a high-tech enterprise recognised by the state.
.jpg)
Sinoma-EC has designed low-temperature WHRPG systems for more than 400 cement kiln production lines at home and abroad, taking the lead with a domestic market share of 30%. In the international market, Sinoma-EC has actively implemented China’s outward-facing ‘going out’ policy and national ‘Belt and Road’ initiative. One of the earliest companies in the domestic industry to enter the international market, Sinoma-EC has now become a leading service provider in the international markets of WHRPG for cement production.
The innovative technology that enables WHRPG
Sinoma-EC has long been at the forefront in terms of scientific and technological innovation and progress of WHRPG. As a subsidiary product of the cement production line, WHRPG technology has previously played the role of an optional addition to cement production projects. In researching WHRPG for the latest generation of cement kilns, Sinoma-EC has worked to break the shackles of traditional conceptions of this technology, turning it from a non-essential production enhancement to one that is a necessity in any cement plant. The company has pushed for WHRPG to be integrated into the design of boiler layouts in the development of any new cement production lines, improving boiler layout and equipment performance.
.jpg)
The latest generation of cement kiln WHRPG technology organically integrates WHRPG with the clinker production line process, and makes the Air Quenching Cooler (AQC) boiler run in series with the production line, so as to make full use of the wasted heat of the flue gas and ensure the safe operation of subsequent processes such as dust collection. In terms of layout, the AQC boiler shares the foundation and platform with the cement production line. The AQC boiler occupies the bottom air inlet, which is directly arranged above the grate cooler and connected with the middle tapping. The air inlet duct is short, the temperature loss and pressure drop decrease, and the system operates very smoothly. In addition, since the AQC boiler occupies the bottom air inlet, the dust in the flue gas falls directly into the grate cooler due to gravity, removing the necessity for the dust hopper, air lock valve, chain conveyor and other dust unloading equipment. Effective measures can be taken for the air intake duct of the AQC boiler to ensure that the flue gas temperature at the boiler inlet can be quickly reduced under abnormal kiln conditions, so as to prevent damage to the AQC boiler duct and body due to the HT conditions. In addition, flow distribution plates and anti-wear covers are set in many positions inside the AQC boiler, which can further prevent the big granular clinker dust entrained in the hot gas from flowing into the boiler body, slowing down the wear of the heating surface and ensuring the heating transfer effect.
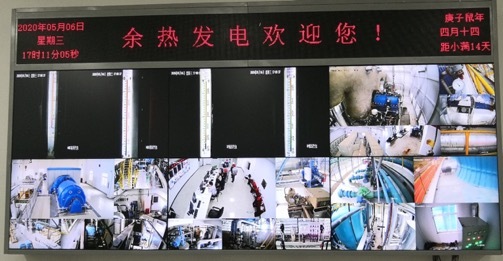
The WHR boiler at the preheater (PH boiler) takes gas from the outlet of preheater C1 and operates in series with the kiln system. The flue gas is induced into the ID fan after heat is exchanged through the PH boiler from top to bottom, and the bypass gas duct is arranged outside the PH boiler. Considering the heat requirements for processes such as raw mill drying, the PH boiler is fitted with a double-pressure system, and the exhaust gas temperature is ≥ 180°C and controllable.
Improving efficiency and ensuring operational stability
With the generalisation of the latest cement clinker calcination technology, the Generation 4 grate cooler, equipped with a central roller crusher and six-stage preheater, has gradually become the normal configuration for the new type of cement plant. In view of such upgrades to the cement production process and its equipment, Sinoma-EC actively explores new WHRPG technology seeking to develop energy-saving equipment. For example, in the situation that the outlet temperature of a six-stage preheater C1 becomes low, the latest generation of WHRPG technology adopts the combined superheating system and uses the hot air in the clinker cooler to reheat the low-quality steam generated by the PH boiler, in order to realise the multi-stage utilisation of wasted heat and effectively improve the thermal cycle efficiency of the power station. In order to maintain the vacuum of the condenser, the latest generation of WHRPG technology uses the full-automatic liquid ring vacuum pumping device, independently developed by Sinoma-EC, equipped with a high-efficiency vacuum pump and condensation system, and establishes communication with DCS through PLC control, enabling automatic operation whilst saving energy and water. All of these measures have laid a solid foundation for improving the overall efficiency of the TG unit and ensuring the safe and stable operation of a WHRPG station.
.jpg)
Saving manpower and increasing efficiency
Sinoma-EC actively explores new advanced level automation and intelligent technologies for use with WHRPG. The latest generation of the WHRPG system features advanced wireless communication technology to collect the operational data from the system, enabling remote data analysis and management. Furthermore, cameras are installed offering the ability to monitor the whole WHRPG system. As such, operation and maintenance guidance can be given in real-time. In order to reduce the number of fixed personnel required to run the system, the latest generation of the technology is equipped with a large number of motorised or pneumatic steam and water valves, an on-line steam and water sampling system and automatic dosing device for the WHR boiler drum. By optimising the regulating circuit and DEH system of WHRPG, there is automatic control of unit impulse starting, speed-up, warm-up, grid connection, load regulation, normal shutdown, and other processes. The above measures are helpful to realise a one-key start to the subsystem and greatly improve the automation and intelligence level of WHRPG station.
Current implementations
Sinoma-EC has built a number of benchmark cement WHRPG projects. The Huzhou Huaikan WHRPG project, which was built for a 7500 tpd cement clinker production line, was planned and constructed under the national implementation of the sustainable development strategy and the comprehensive resource utilisation policy. This WHRPG project boasts Sinoma-EC’s shortest construction period, highest automation procedure and industry-leading comprehensive index. Since the trial operation of the Huzhou Huaikan project at the end of 2019, it has been running well. On the premise that the per unit heat consumption of clinker is 638.82 kcal/kg and the comprehensive power consumption of clinker is 40.31 kWh/t, the power generation per ton of clinker is more than 29 kWh/t, which is better than the assessment index, and has reached the best level in the industry among the cement clinker production lines equipped with six-stage preheaters. The project’s advanced automation equipment allows for the greatly reduced use of labour, and significantly improves work efficiency. High quality equipment maximises the recovery of wasted heat, reduces energy consumption, and increases power generation. The power consumption ratio of the station is also maintained at a low level, maintaining Sinoma-EC’s service tenet of ‘low energy consumption and high output’.
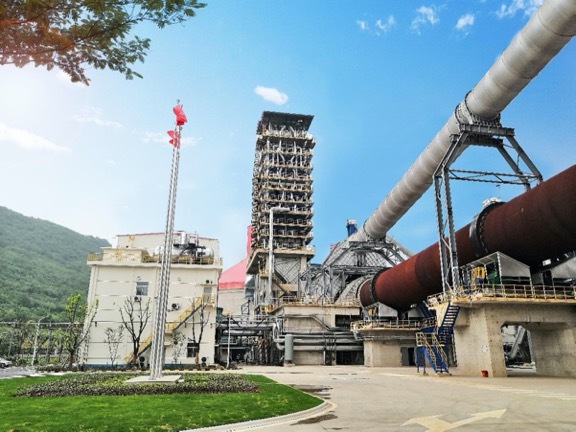
The Tongchuan Yaobai WHRPG project is a set of low temperature WHRPG units supporting the first intelligent 10 000 t demonstration production line in the western region of China, with an installed capacity of 15 MW. As the production line with the most advanced technology, the highest environmental protection level, and the highest construction standard in the development history of Yaobai, Tongchuan Yaobai is positioned at the forefront of the technological development of the global cement industry with intelligent energy saving as its core principle. As an important part of the demonstration line, the WHRPG system undertaken by Sinoma-EC uses the latest generation of WHRPG technology, organically integrating the WHR boiler with the cement production line, exhibiting results that the WHRPG per tonnage of clinker is greater than 28 kWh/t.cl.
Energy conservation and emissions reduction promoting green development
Chairman Xi Jinping delivered an important speech at the 75th General Debate of the UN General Assembly, stating that “China will enhance the country’s independent contribution and adopt more effective policies and measures. Carbon dioxide emissions will strive to reach a peak by 2030, and strive to achieve carbon neutralisation in 2060”. Since then, the first year of ‘Carbon Neutralisation’ has been officially opened. Sinoma-EC, as a listed company platform with specialised technical services for energy saving and emission reduction under CNBM (China National Building Material Group Co., Ltd.), has previously put into operation a WHRPG project with an annual power generation capacity of 24 billion kWh, which can reduce carbon dioxide emissions by 20 million tpy, equivalent to 7.6 million t of coal.
Driven by the goal of China’s ‘double carbon’ policy, Sinoma-EC is investing in the development of new low-carbon technologies, green materials and environmental protection equipment, whilst building a new model of ‘Source-Network-Load-Storage’ integration and multi-energy complementarity. This includes the R&D of new clean energy technologies, the development of compound energy storage technologies for industrial heat and power storage, the promotion of CO2 capture, utilisation and storage technologies, new green wall material, calcium silicate board, production process innovation and the development of the manufacturing of high-efficiency photothermal equipment, etc.
Summary
Sinoma-EC has been striving to achieve the breakthrough of ‘zero’ outsourcing power of the cement clinker burning system. In this regard, the company has strengthened R&D, studied the recovery and utilisation of low-grade wasted heat, so as to maximise the utilisation rate of waste heat resources in the whole plant. At the same time, according to the structural features of the cement clinker burning workshop, 5G ‘big data’ application technology and a number of new green and low-carbon technologies such as solar, wind, and geothermal energy as well as energy storage have been introduced. Further improvements to the intelligence level of the overall WHRPG system can help reduce the dependence of the burning system on the power supply of the Power Grid, so as to maximise the ‘Power Neutralisation’ of the cement clinker burning system and achieve the goal of energy saving and carbon reduction.
Read the article online at: https://www.worldcement.com/asia-pacific-rim/02112022/integrating-green-intelligence-into-whrpg/
You might also like
The World Cement Podcast - CleanTech & Venture Capital
Our guest for this episode of the World Cement Podcast is Alfredo Carrato, Venture Capital Advisor for CEMEX Ventures. Listen in to the conversation as World Cement's Senior Editor, David Bizley, and Alfredo discuss the role of venture capital and cleantech in enabling the cement industry's green transition.
Tune in to the World Cement Podcast on your favourite podcast app today.